Photo credit: Nathaniel Riley
Working @ MATT – Assistant Project Management
What's it like to work at MATT?
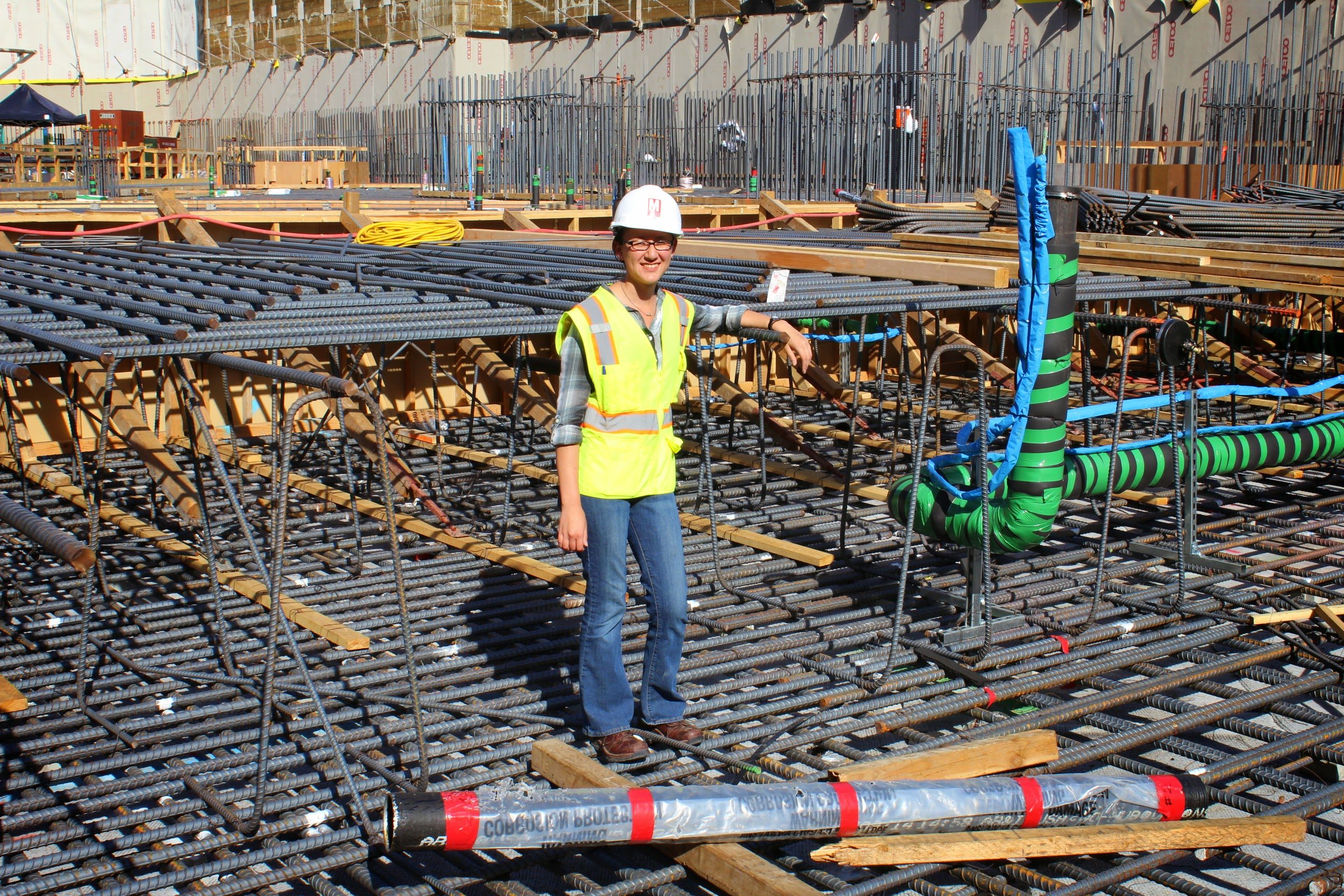
Many Paths, One Ladder
Cory Kuo grew up in Taiwan, the child of two civil engineers. Wendi Gilbert worked on three major projects with MATT as an architect before crossing over to construction. Graham Whaley’s father worked at MATT Construction for years before Graham joined the family. Jon Ou spent time in landscape construction in Pennsylvania before he transitioned to general contractor work. Jen Sliwa studied civil engineering at Purdue, interned at MATT to get field experience one summer and never looked back. Kendall Crossley grew up remodeling homes with his family and loved it so much that he studied construction management and development through the graduate level.
Six different MATT employees all found their way onto the PE-SPE-APM-PM-SPM-VP track from six different walks of life. What they all share is a love of being in the field, the challenges MATT provides to its people and the satisfaction that comes from seeing the buildings they’ve helped to shape come to life before their eyes.
Photo credit: Nathaniel Riley
Building Blocks: What It Takes To Become An APM
As employees move up the ladder from being project engineers to senior project engineers, they learn the nuts and bolts of construction. Daily duties build the fundamental principles for a life in the industry. “As a PE, you’re trained to understand what construction is,” Cory explains. That could include writing RFIs, visiting the jobsite, reviewing shop drawings, overseeing scheduling and procurement, assisting superintendents and whatever critical issues may arise. Other tangible concerns like “concrete height or door fittings” could make up much of the daily preoccupation for a PE, according to Graham. Jen adds, “PEs focus largely on task-related skills. You learn the ropes, you learn how processes work, you learn how to do things that get a building up and keep the process moving.”
On every MATT site, Cory notes, “everyone works as a team. But as a PE and SPE, you’re working more on details to understand how every item pieces together.” SPEs gain mastery over the essential skills they’ve been cultivating, working their way towards the APM list of responsibilities. They focus more on submittals of material data, samples, product data, requests for information (RFIs), procurement and keeping things on track. Establishing a rich knowledge base is essential. Jen says, “If you don’t understand what the processes are, it’s harder to understand why they’re important and how to keep the job moving.”
“Hands down, the most important thing I learned from being a PE and SPE is quality control,” Kendall believes. “Other than vetting subcontractors, the first opportunity for the GC to inject quality control into our projects is the project submittals. They can be very tedious, but they are the pulse of the project. The project can’t be built without submittals, and the more quality control we invest in the submittals, the better the project progresses, the better the end product becomes.”
Jon feels that he experienced the “ideal process of development,” starting out in the estimating department and working his way to construction. That is what he calls “the natural process of any project. You can’t build before you estimate.” Getting that experience helps employees move naturally into bidding, negotiations, preconstruction and finally “sticking a shovel in the ground.”
Photo credit: Nathaniel Riley
Beyond the nitty gritty of daily jobsite needs, Graham appreciated watching his superiors in action and learning from them. “I was lucky to witness a lot of good PMs, senior PMs and VPs in action with owners.” Their example provided early guidance on how to navigate tough discussions and decision-making moments that come up on any project. He learned to tailor the approach to different scenarios. Understanding “how to deliver a message” while finding a way forward that works for everyone is a delicate art, and Graham feels grateful for the exposure he had to experienced higher-ups handling their projects with grace, expertise and conviction.
Graham also appreciates MATT’s ability to gauge its employees and their readiness for progressing in their careers. “MATT has a good temperature read on the individual in regards to the position they’re in to make sure they’re not promoted prior to when they should be or given more than they can handle. I always take the opinions of my superiors very seriously. They’ve already lived it and been through it, and I respect that. When you are ready, you are ready.” MATT works hard to deepen employees’ capacity so that on any given project, “even if you don’t know what’s coming, you have the experience to deal with it, even if you’ve never done it before.”
“You don’t become an APM to do APM-level stuff,” Jon shares. “You’re an APM to learn how to do PM-level stuff.” The evolution and aspirations that help employees to progress benefits both the individual and the company.
Daily Life As An APM
“Each project presents unique challenges and obstacles,” Kendall reflects. “The opportunity to work with your team to find creative solutions and answers to these challenges is probably my favorite aspect of construction management.” From “hoisting a 50-foot-tall intercontinental ballistic missile into a vertical position for an art installation, to managing the logistics of building a swimming pool on top on an 18-story high-rise in a rainstorm, to demolishing the center of an active parking garage in order to build a 34-story high-rise right through the center of the garage,” the stakes are both enormous and exhilarating.
Moving up to the level of APM and beyond, as Jen reflects, “you begin to take more focus on decision-making, the purpose of processes. You’re exposed to more risk management and making decisions about where there is risk, both in the budget and the schedule. You negotiate with contractors, manage relationships with clients and the design team.” Part of the shift from being a PE and SPE, where major decisions tend to lie with someone higher up, to an APM is that “you begin to have a little more latitude in making judgment calls and knowing you have the knowledge base to do that. You do take on more responsibility for people. For newer PEs, you can have more of an advisory role.”
Being a guide to PEs and SPEs has been a rewarding aspect of the APM role for Cory as well. She loves “being a trainer, making sure PEs and SPEs are on track with their duties so that everyone can work as a team to assist the the PM. We’re all here as a team.” With every member properly briefed on how to get the job done, operations flow efficiently. Passing down skills learned from her own experience is a recurring theme for each stage of evolution on the jobsite. “Everyone gains knowledge every day,” she believes, regardless of what level they’re currently occupying.
For Wendi, who had spent twenty years working as a project architect before joining MATT, the transition to APM wasn’t difficult. After she had grasped the coordination of trades and critical contractual elements in documents, navigating negotiations and understanding the ins and outs of management came easily. Now, she’s working on the same project she helped to shepherd from the architecture side, and many of the same people are on board, albeit in different positions. Working with her own former architecture team and MATT colleagues, there’s already an established language and trust that facilitates the process.
Another key part of an APM’s responsibility is in “cost-related matters and seeing items in their big-picture context,” Cory adds. Identifying a range of possible building materials, for example, versus understanding why one of those materials would harmonize best with vision, scope and budget separates PEs and SPEs from the APMs. At the higher levels, MATT’s employees begin to take ownership over major project choices.
Jon now handles cost-related issues while also managing PEs and ensuring that they understand their priorities and expectations, delegating responsibility for the fine detail stages of a project. Details filter up from peers in the PE and SPE positions, and the APM’s job is to put everything in perspective and then report upward so that PMs, SPMs and VPs can speak intelligently to big-picture matters with the design team and client. APMs effectively serve as liaisons for the team members above and below them.
Kendall’s favorite phase is “during construction, when we are able to be in the field and watch the project come together. The actualization of the conceptual ideas and plans, and seeing our investments pay off, is very rewarding.” The further up the ladder employees climb, and the more responsibility they have, the more fulfilling it can be to watch their hard work and choices come to fruition before their eyes.
What MATT Does Right
“They’re builders,” Wendi recognized from her many years of collaborating with MATT on the architecture side. “They’re a family you want to belong to. If an architect feels like this is a team that’s willing to come to the table and assist, that speaks volumes for the culture of the company. It’s about doing the right thing and getting it done right.”
“Working for MATT is like being called up to the Big Leagues,” shares Kendall, who has always loved building things with his hands and has therefore (unsurprisingly) spent more than half of his life working on various types of construction sites. “The way MATT thinks, operates and executes is at a completely different level. Everything from procurement, to contracts, to closeout and even how MATT conducts meetings is impressive.”
The type of projects MATT pursues and attracts makes it an especially appealing general contractor to work for, everyone agrees. “There will never be another one like this” is a regular sentiment on the jobsite, according to Jen. “Iconic buildings on the LA landscape that we helped make happen” leave a strong incentive to go above and beyond. Jon loves “the caliber of project that MATT takes on with flashy and funky architecture. There’s never a dull moment, “but rather a constant wave of challenges and creative thinking.”
Most of the construction work Cory did before joining MATT was public sector-related, such as airports, schools and hospitals. MATT’s approach, pursuing private-client jobs through negotiated GMPs and leveraging a strong history of relationships with subcontractors was a major draw for her when choosing the next step in her career. “There’s also more direct teamwork with the architect and client as the group comes up with the best solutions to proceed with the work down the road.” Jen adds that “negotiated work rather than hard bids creates an interpersonal environment that’s very different. You have motivation to build relationships in order to get the job done. It’s not just about the money. It’s about invested industry relationships,” with real stakes and real collaboration.
“Relationships are so important in our industry,” Jen reflects. “A lot of people who start out in construction may be surprised to find that so much of our success depends on building relationships with clients, subcontractors and design team members.”
Jon finds comfort in the “driving power MATT holds. We want to serve clients and tailor to their needs, but we still hold authority over the direction that makes the most sense for the project.” The relationship between owners, architects, representatives and the general contractor can be delicate, and working with MATT has helped Jon to understand its nuances. “Ultimately, everyone works for the owner. We have to work together. Our responsibility as the general contractor is to put the schedule down, the milestones in place, and then make sure the team doesn’t allow those to be missed.”
The emphasis on working relationships applies internally, as well. For Cory, MATT’s family style sets it apart from other top-tier general contractors. “You know everyone and work as a family, helping each other. MATT takes care of you.” Graham further explains, “As a company, MATT backs its employees on their decisions. As long as they understand the logic that went into it,” whether it was the best call or not, they will appreciate and support the process of employees learning and growing. “In construction, there are so many opportunities for something to go wrong. Those scenarios come up, and it’s nice to know that your superiors have your back.”
“Being able to solve puzzles and work through conflict is rewarding and one of the reasons I got into civil engineering,” Jen shares. She enjoys construction itself, but one of the most thrilling moments is afterwards, “when you really have a physical monument to the work you’ve put in, when you can stand on a street corner and look up at a building and know that you helped get that physically up off the ground.”