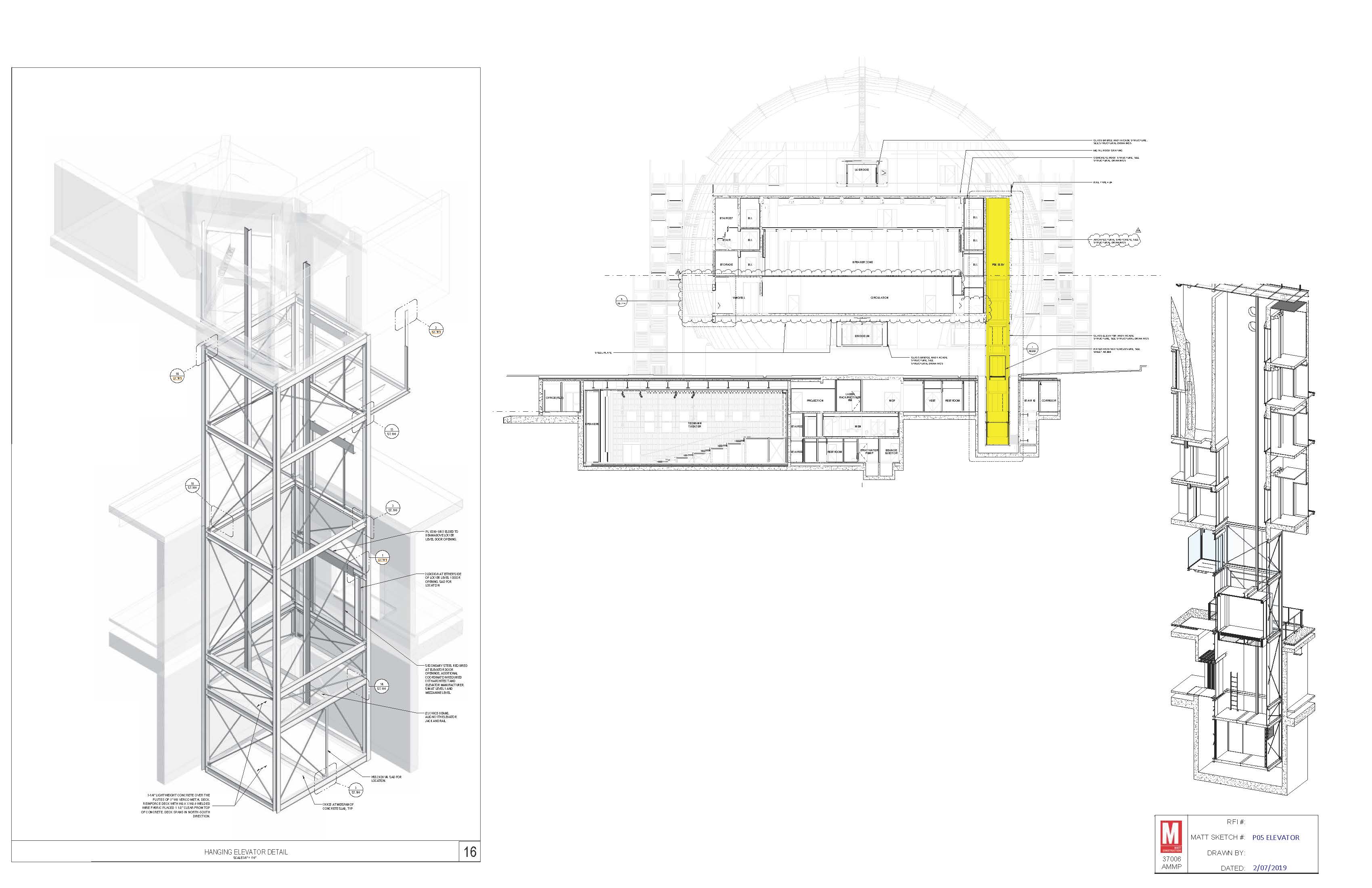
Location
Los Angeles, CA
Owner
Academy of Motion Picture Arts and Sciences
Design Architect
Renzo Piano Building Workshop
ViewHanging Out At the Sphere: How MATT’s Team Built a Hanging Elevator System For the Academy Museum’s David Geffen Theater
MATT's Team Builds a Unique Hanging Elevator System for the Academy Museum of Motion Pictures
As the Academy Museum of Motion Pictures nears completion, some of its final—and most challenging—design elements are taking center stage on the jobsite. Chief among those is the hanging elevator system being installed in the massive spherical David Geffen Theater attached to the main museum. Numerous other trades and finishing details depend on the elevator being finished, making it a time-sensitive priority.
Suspended Elevation: Why Hanging Elevators Are Different
The David Geffen Theater’s unique roped hydraulic elevator adheres to the basic elements required by many of its counterparts. Every elevator is located near its machine room and sits in a hoistway stacked from a pit. But not every elevator hangs. Because of its home in a base-isolated sphere, which has been designed and built to stand still if the earth moves during seismic activity, the elevator is attached to the top of the structure housing the Geffen Theater.
A standard hydraulic elevator requires a deep jack hole for the piston to push the cab up and down, which would require seismic joints around the upper levels of the hoistway, which would in turn require a larger void space within the Geffen Theater plus added depth for the hydraulic cylinder. The Geffen Theater elevator’s design circumvents this need. Containing the roped hydraulic’s components within the hoistway allows the slab to be disconnected from the surrounding grade so that the elevator can be suspended and ride with the Geffen Theater’s base-isolated structure. In effect, it’s not unlike a forearm dangling from an elbow off of a horizontal upper arm. If an earthquake strikes, the elevator system will remain static in the space rather than being shaken.
Another unusual challenge of the suspended system came in the form of identifying where to place the elevator’s control room. Typically, one would not install a control room in the hoistway itself. In this case, however, having the control room beneath the elevator in the suspended hoistway provides a more convenient and elegant solution to the unique design. Because the control room rides with the elevator, it will behave the same way as the elevator itself in case of an earthquake. The team provided a seismic gap around the entire hoistway, giving it a certain amount of space to move. With the elevator equipment and machinery attached directly beneath the cab rather than several feet away, there was no need to connect the control room to the elevator through the seismic joint—a flexible connection used to create space between adjacent buildings or parts of buildings to accommodate for possible movement. Fewer elements requiring a flexible joint creates far fewer headaches for the team, so attaching the control room to the cab saved in time and hassle.
Timing Installation: How the Team Scheduled and Sequenced Multiple Trades Around Elevator Construction
As one of the final and most complicated elements to go in, the elevator system itself has dictated the coordination of multiple trades. Before the elevator work could even begin, the sphere had to go up around the location and be stabilized. A critical tower crane occupied the space adjacent to the elevator pit, meaning the hoistway’s installation needed to be sequenced after the crane and dome glazing shoring were removed, leaving the sphere self-supported on its four pedestals with base isolators.
Scheduling and material lead times for the hoistway installation precluded the option of measuring the hoistway’s glass lites and aluminum panels in the field. Additionally, the elevator manufacturing company handling the installation follows specific codes and requirements, guided largely by safety, which prevent anyone from being in the space above their team and the open shaft during their part of the process. They required that the entire hoistway already be in place and enclosed before their work on installing the cab, machinery and other components could begin. It would then take an estimated 20 weeks to complete the job.
All of this left little time for the glasswork and the aluminum honeycomb finish panels. The suspended system requires supportive cross-bracing to make sure it does not lose its square shape as the team continues to piece it together. Further, because of the cross-bracing the aluminum panels need to be installed from the interior, and thus in place prior to the elevator install. Because of these constraints, getting structural steel, mixed metals and other trades dialed in and agreeing on tolerances and surveying alongside actual construction, required meticulous planning and clear communication. MATT and the subs came together to determine what tolerances the ironworkers could hold and to guarantee opening sizes, which in turn allowed the glass and aluminum hoistway cladding subcontractors to begin fabrication. They also surveyed the steel frame while it was being erected to ensure that the dimensions were on track. Through this concerted planning effort, all of the panels arrived in time and ready for installation.
Subcontractor Stories: Plas-Tal’s Perspective On the Elevator’s Steelwork
One of the key trades involved in building any elevator is structural steel. MATT worked closely with Plas-Tal Manufacturing, a union steel fabricator and erector that has served California for over six decades. Plas-Tal’s CEO, Sean Brunton, has played a critical role in budgeting and design feedback for the elevator since 2015. He commented on the particular nature of this elevator’s challenge: “It’s weird in the sense that it’s hanging, and you have to keep it straight.” To mitigate the possibility that it might “rack to the side” during construction, crew members in the field braced the structure off.
Brunton, like many others on the team, approached this first-time design challenge with enthusiasm, embracing the problem-solving skills it demanded. Logistically, the hardest element to troubleshoot was getting the cage itself into the space. At roughly 40 feet long, with a 20-foot gap between the bottom of the building and the concrete to drop the cage into the pit, the crew could not fit the cage into the space in one piece. Instead, they cut it into smaller pieces and slipped the materials into the hole, an efficient solution that kept access intact. Maintaining the alignment of unusually small members—another architectural feature of the elevator—over a 40-foot space presented another steel challenge. The team carried it out with painstaking precision and constant vigilance.
Embeds are steel plates that attach the structural steel frame to the concrete and support the hanging columns. The embeds for the elevator shaft were cast into the bottom of the slab of the Geffen Theater’s structure. The hoistway itself needed to be centered within the pit to allow for movement on all sides. Over the course of work, the building was projected to shift slightly, which would lead to the embeds no longer being directly above their designated points. Because the elevator shaft’s position could not change, the team had to devise a special way of attaching the columns to the embeds while keeping the opening the same size. Anticipating the need for adjustment, they had already built tolerances into the overall height of the hoistway’s steel to allow for steel plate shims to be installed. This made the adjustment for the embed connections possible.
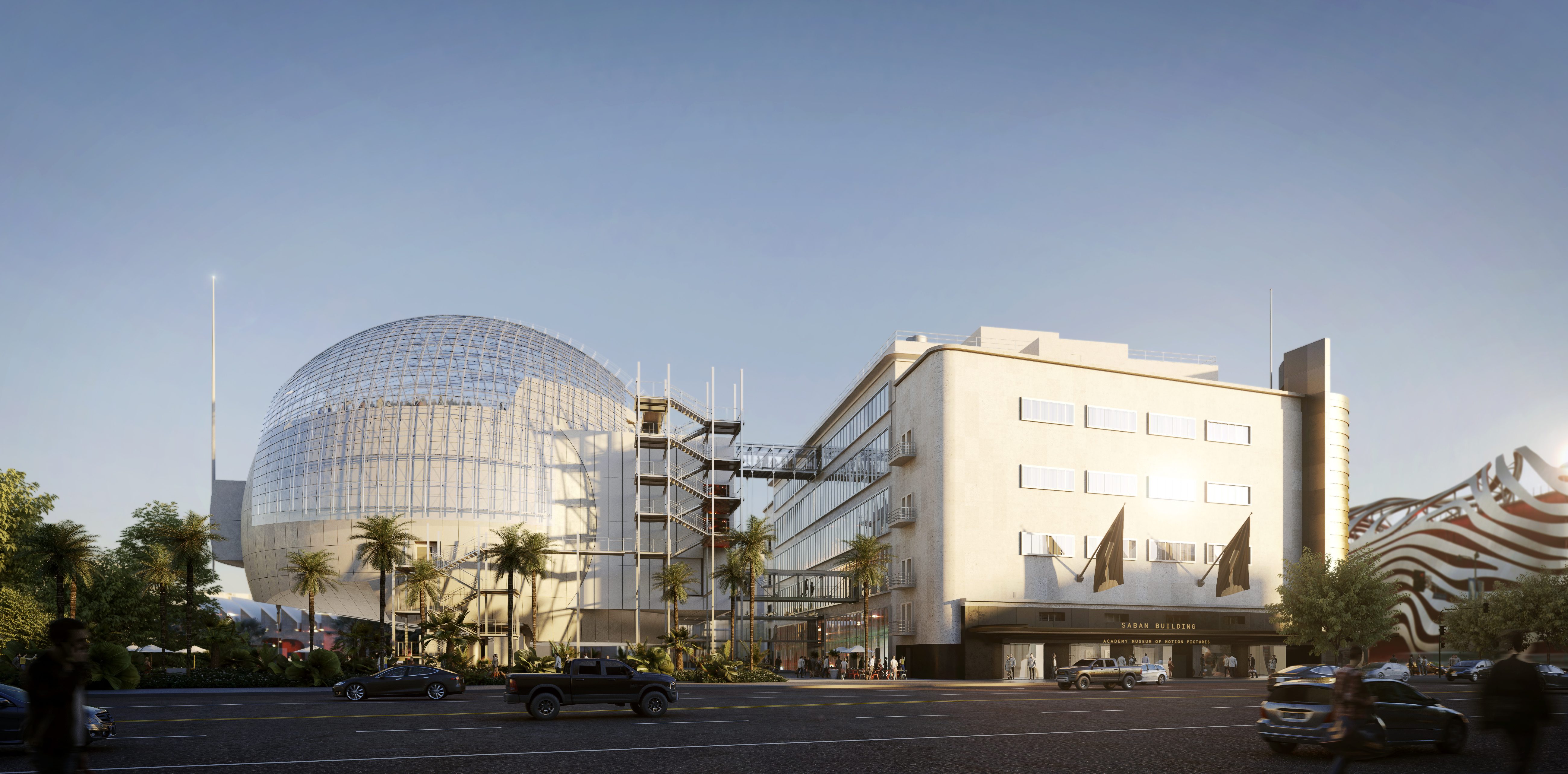
Rendering credit: ©Renzo Piano Building Workshop/Images ©A.M.P.A.S./Images from L’Autre Image
Ramping Things Up: Making Fast Moves On the Jobsite
For the first nine months of construction, the team went back and forth with drawings of the elevator. Not until the end of month eighteen, when the site was nearly ready for the elevator work to begin, did the task become more tangible—and more pressing. After incorporating any new or unexpected developments from the previous year and a half of construction, the drawings received final approval in December of 2018. Steel fabrication happened during January of 2019, with installation happening at the end of January and throughout February. Panels and glass were installed in March, with finishing touches ongoing through the end of the project schedule.
Because they are so rare, this effort represents the first time most of the crew members have tackled a suspended elevator system. But it’s not the only challenging first for MATT and colleagues, who thrive on unlikely designs that demand broad vision and rigorous execution. The drive to find the best and boldest in their respective trades provides MATT with a continually growing network of partners in the field who relish the opportunity to see iconic architectural features come to life. For an example of another first, read the story of Caltech’s Center for Autonomous Systems & Technologies