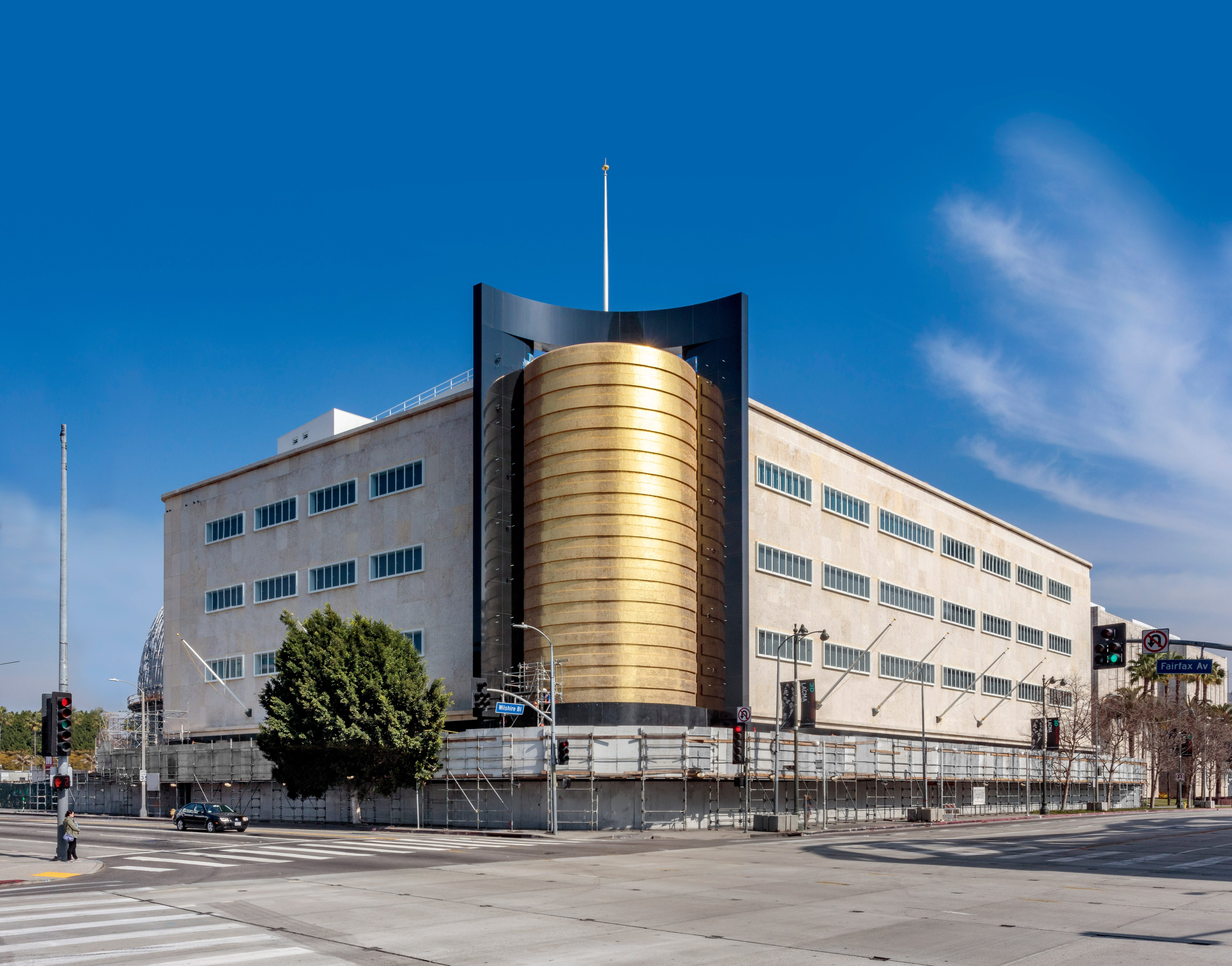
Photo by Joshua White JWPictures/©Academy Museum Foundation 2018
Location
Los Angeles, CA
Owner
Academy of Motion Picture Arts and Sciences
Design Architect
Renzo Piano Building Workshop
ViewHistoric May Company Building Undergoes Major Restoration and Transformation into Academy Museum of Motion Pictures Saban Building
Renzo Piano Building Workshop, Gensler and MATT Construction Teamed Up to Restore and Revitalize LA's Historic May Company Building, Now the Academy Museum of Motion Pictures Saban Building
LA’s treasured Wilshire May Company building has received a second lease on life through its reincarnation as the Saban Building, part of the landmark new Academy Museum of Motion Pictures set to open its doors in 2020. Situated in good company near the Los Angeles County Museum of Art (LACMA), the Petersen Automotive Museum and the LA Brea Tar Pits and Museum, the Academy Museum will be a fitting addition to Wilshire’s museum corridor.
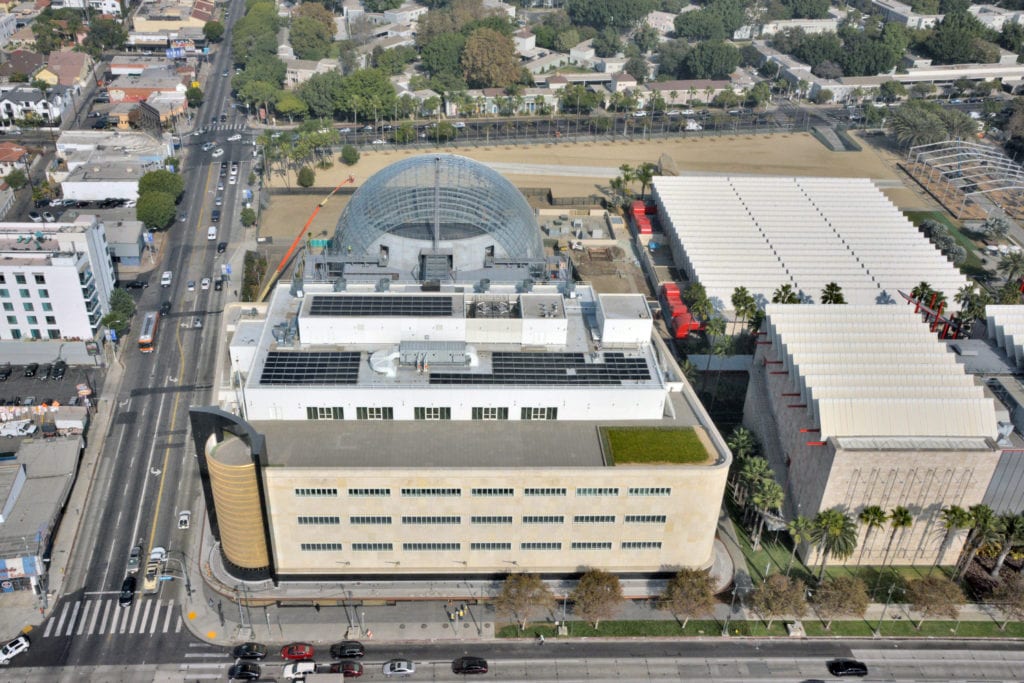
Rescue Ops: Los Angeles Conservancy Protects May Company Building From Demolition
Influenced by the Streamline Moderne style popular in the era from 1929-1946, typified by industrial, nautical and aerodynamic themes, the former May Company building represents an important contribution by noted architect A. C. Martin and Associates, alongside architect Samuel Marx, who came together in 1938 and built the store in 1939. Its eye-catching southwest corner hemi-cylinder, clad in Italian gold-glass mosaic, was designed to attract suburban motorists. The fact that it was the first May Company building outside of downtown further bolstered its significance in the LA cultural landscape.
The building’s logo, painted on its wall even during its construction, reflects the service-oriented ethos that solidified it as a welcoming nexus, catering to customers’ shifting needs: “The May Company Wilshire…dedicated to the shopping comfort and convenience of Greater Los Angeles.” But despite its steady presence, disuse led to endangerment. One of the more nail-biting episodes in the May Company building’s history came in the 1990s, when demolition talks began. Knowing that the building had a long relationship with the city, LA Conservancy launched a campaign to rally public support, hoping they could convince Councilman John Ferraro that the building should be saved from destruction.
But what really won the day? The LA Conservancy compiled a book of stories about the role the department store had played in local life for decades. Whether to buy a first pair of long pants or to shop for a wedding dress, the site had become an emotional anchor for the city’s inhabitants throughout major milestones. And as a visual landmark that people walked and drove by every day, it also formed a regular part of their routines, making its state of abandonment all the more disappointing, and making its rejuvenation all the more exciting. The persuasive collection of testimonials earned the building landmark status in 1992.
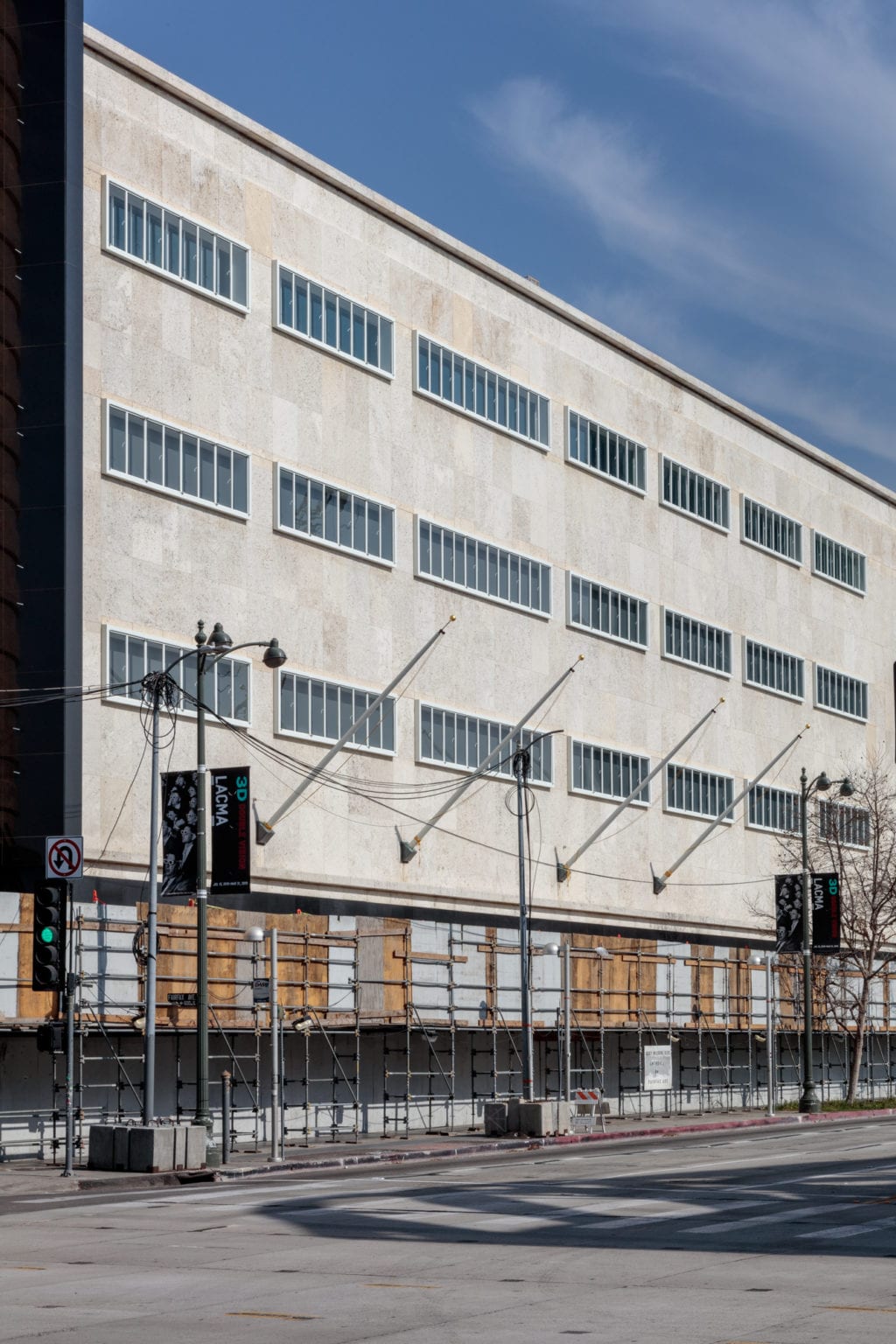
Restoration Ops: Preserving the Historical Fabric
As Superintendent Josh Rosenbeck reflects, this preservation attempt was “unique” and featured challenges that “no one’s ever done before. It was uncharted territory. With historical buildings, you never really know what you’re going to uncover. Just because there’s a set of plans, doesn’t mean something has been built that way. It’s a daily challenge, but that keeps it exciting.”
Analyzing the building’s current condition and identifying the best means to preserve as many exterior elements as possible would not be simple. The limestone cladding panels, black granite pylons and gold-tile mosaic all exhibited symptoms of time’s toll, but they would all require different methods to restore. Recognizing that the challenge required specific expertise, the Academy Museum commissioned world-renowned conservation specialist John Fidler to tackle the exterior envelope of the steel-framed structure. His efforts brought the building full circle with much of its own history.
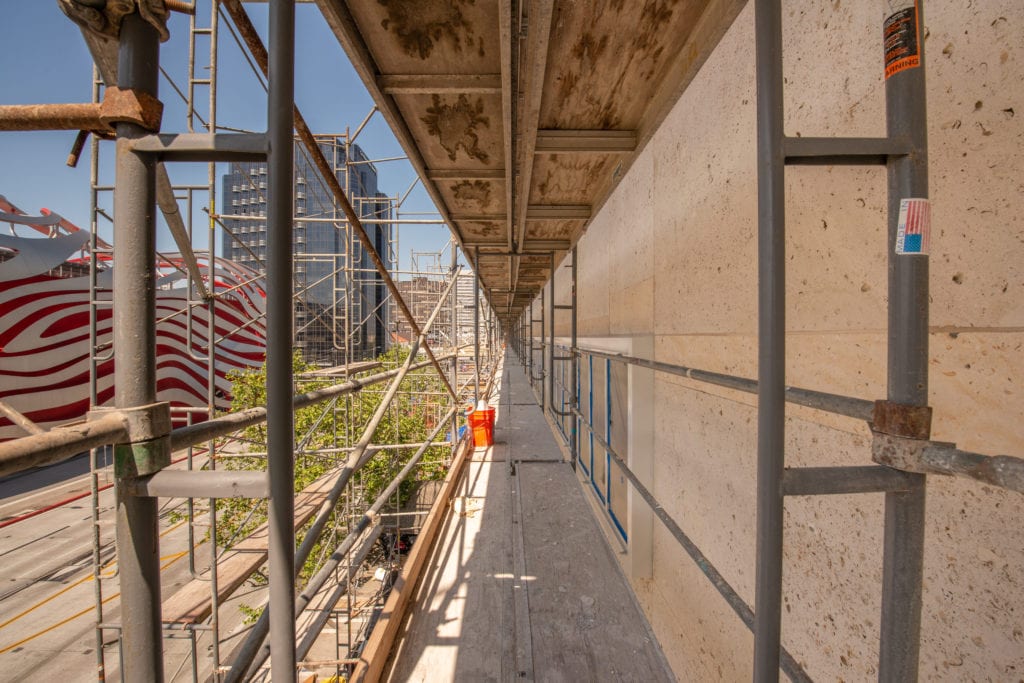
Pioneering Limestone Repair and Replacement
Early investigations of the building found wear and tear that one would expect from decades of use and disuse. The limestone exterior cladding bore cracks and both large and minor spalls above and below joints where the original steel support angles and kerf tab restraints had corroded over time. In total, 1,216 individual limestone panels required stabilization. To achieve this, the team used a pioneering helical friction anchor system to pin the panels in place and thereby bring the building up to code.
Anywhere from 16 to 20 helical anchors went into every panel. Shaped like a drill but with sharp arrises and points at each end, the tapering helical anchors were inserted into narrow pilot holes in the stone all the way into the concrete backing wall and were then locked in place by friction. These corrosion-resistant anchors blend seamlessly into the pattern of natural holes and shell indentions inherent to the Texas Cordova shelly limestone, preserving the façade’s historic character.
To further maintain the original aesthetic, Fidler’s team sourced the new limestone for the Dutchmen — insets that replace a fault in stone with matching material — from the same geologic vein and quarry system in Texas as the original 1939 limestone. Specialized lab testing informed decision-making on how the helical friction anchors would get along with the new stone material, which presented its own aquatic challenges to navigate.
Because limestone soaks in water like a sponge but quickly releases it again, Fidler and MATT had to figure out how to encourage any water that might infiltrate the cladding to then be released to the surface. They devised a continuous flashed waterproofing system that would direct any water that could penetrate the stone back outside under the new Dutchmen repairs. After pinning and adhering the new matching stone Dutchmen on top of the flashing, cladding joints were repointed to match with weep slots left for drainage.
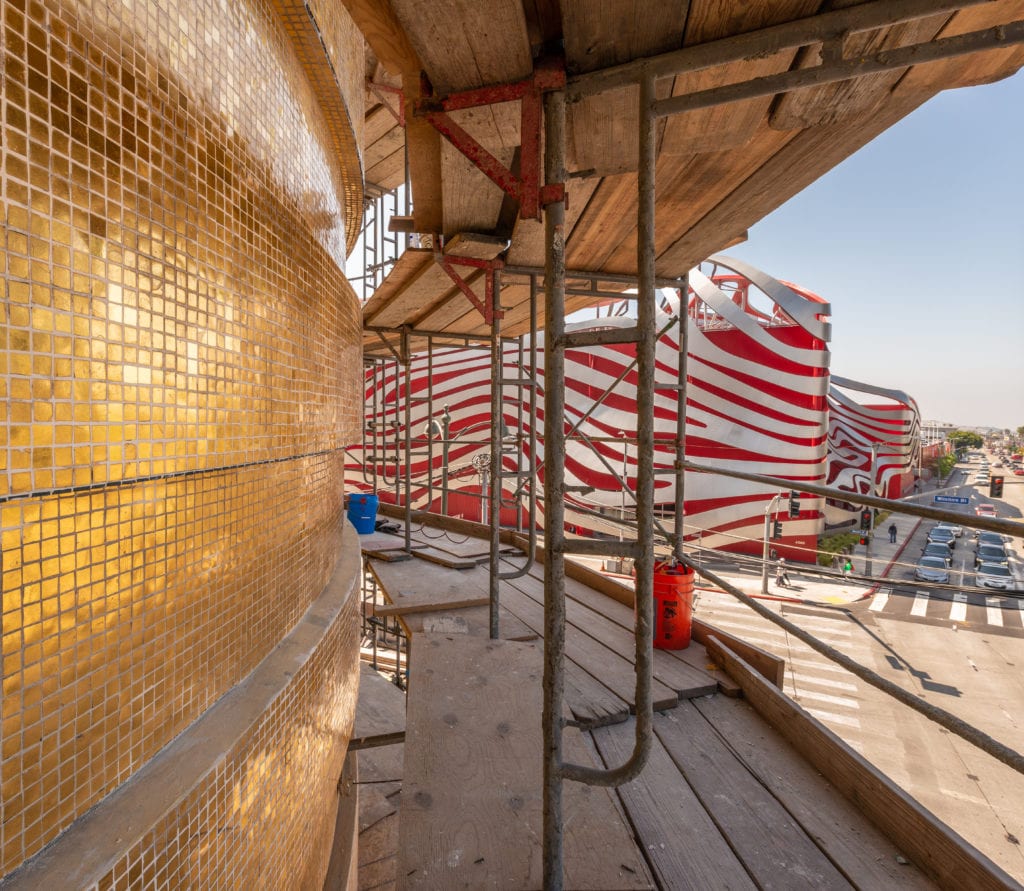
A Tale of Tens of Thousands of Tesserae
The last thing to be scaffolded on site was the most expensive: the southwest corner of the building where the golden glass mosaic has gleamed in the California sunlight for decades. Initial investigations identified chips, cracks, delaminating, soiled surfaces and non-matching replacement tiles. Incredibly, a worldwide search for matching replacement material led to Orsoni, the Venetian glassmaking studio founded in 1888 that had crafted the original tiles.
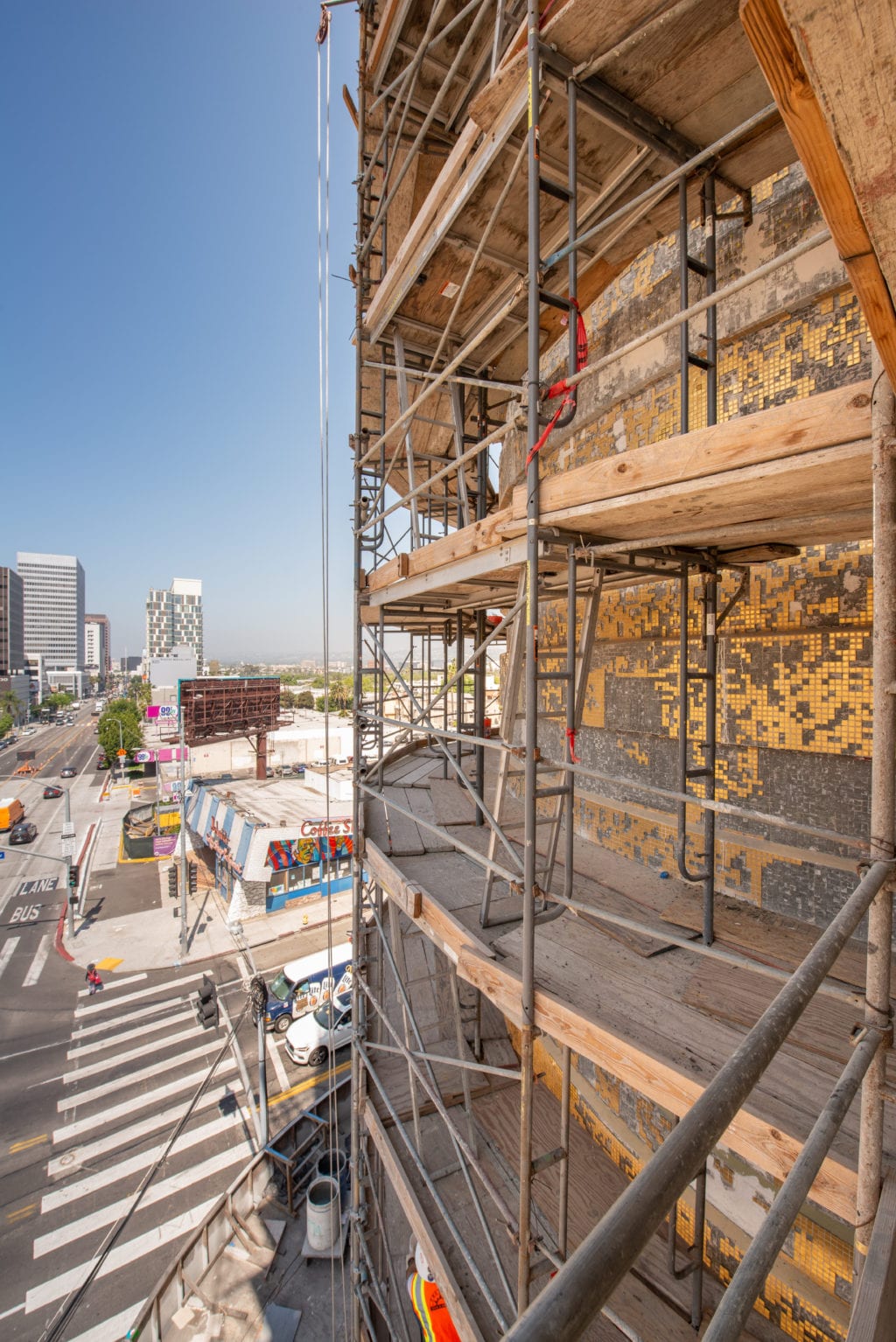
The Orsoni studio still performs all work by hand in meticulous stages: first, they blow the glass into a thin disc, then overlay it with gold leaf, then set a very thin layer on glass atop the gold, then bake it to laminate the whole surface together and protect the gold leaf. Once the sheet is cool, they use disc molds to score and cut the sheet three to four times in each direction, after which they break it apart. Because of the building’s curvature, each one of the nearly 200,000 tiles needed to be set in place by hand. That painstaking process took months, but the isolated position of the building corner made it easy to perform the work without slowing down the rest of the building’s restoration.
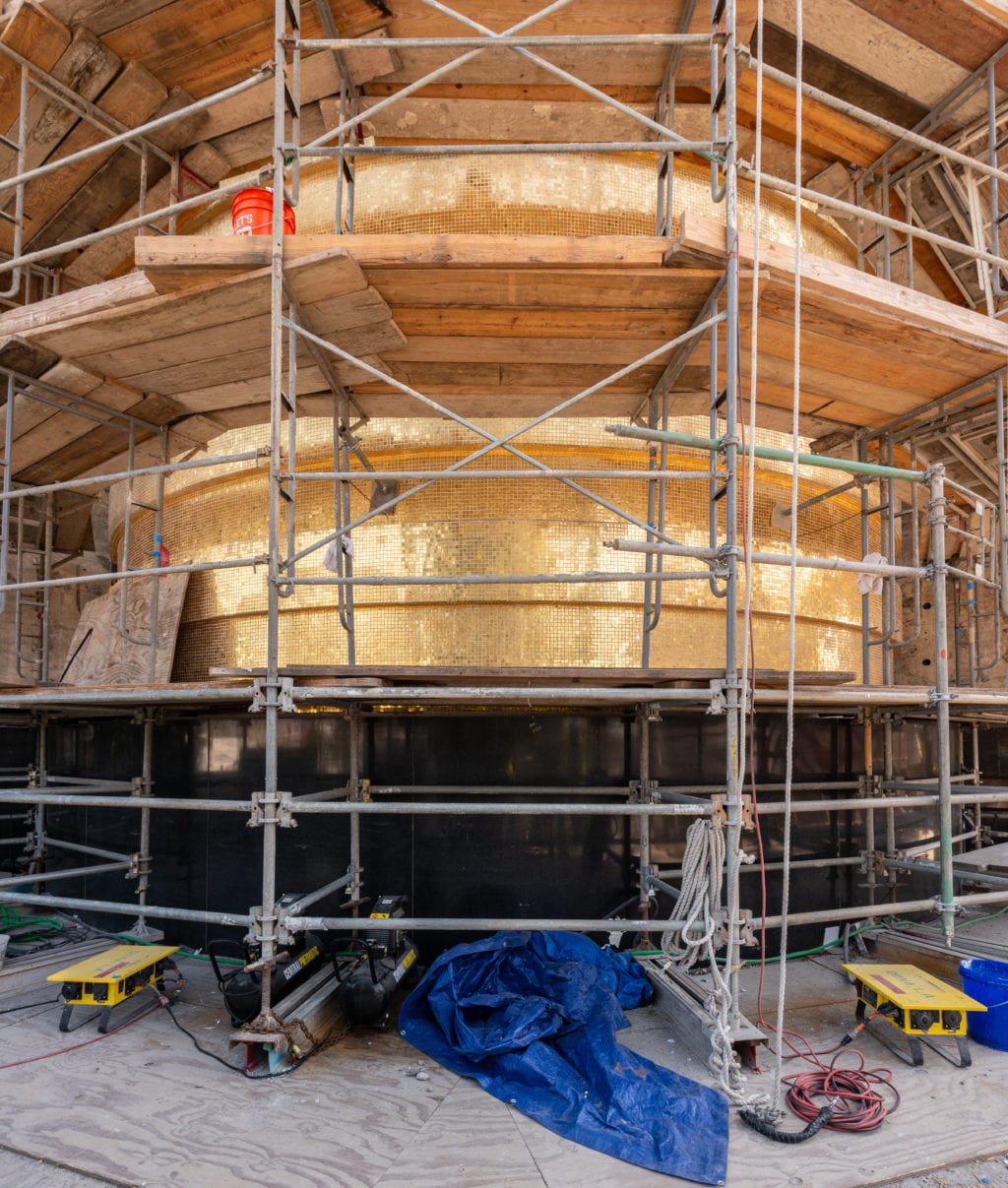
High-resolution imagery provided by GigaPan™ software system helped the team to understand the mosaic’s deformation before scaffolding access, after which traditional knuckle-tapping established a more refined color-coded paper dot system to mark the tiles for retention, grouting, repair or removal. MATT worked with a team to count every tile on the elevation. Qualified conservators instructed tiling crew members on how to complete the delicate removal work using smaller tools, like Dremels loaded with cutting discs, to extract the tiles gently without ripping them off the wall. For the tiles that were to remain in place, the team tested several different types of cleaning solutions and dilutions to make sure the glass would not be damaged.
Fidler went the extra mile to identify a grout color that would match the color of the aged grout already in place and found a single vendor, Laticrete attachment tile supplier, to be responsible for waterproofing, sealing and attachment. Laticrete’s people trained the crew on how to mix the product in small batches and apply it within a narrow timeframe of 45 minutes, before the mix would be unusable. The crew used this mix to the place the new and repaired tiles on the wall.
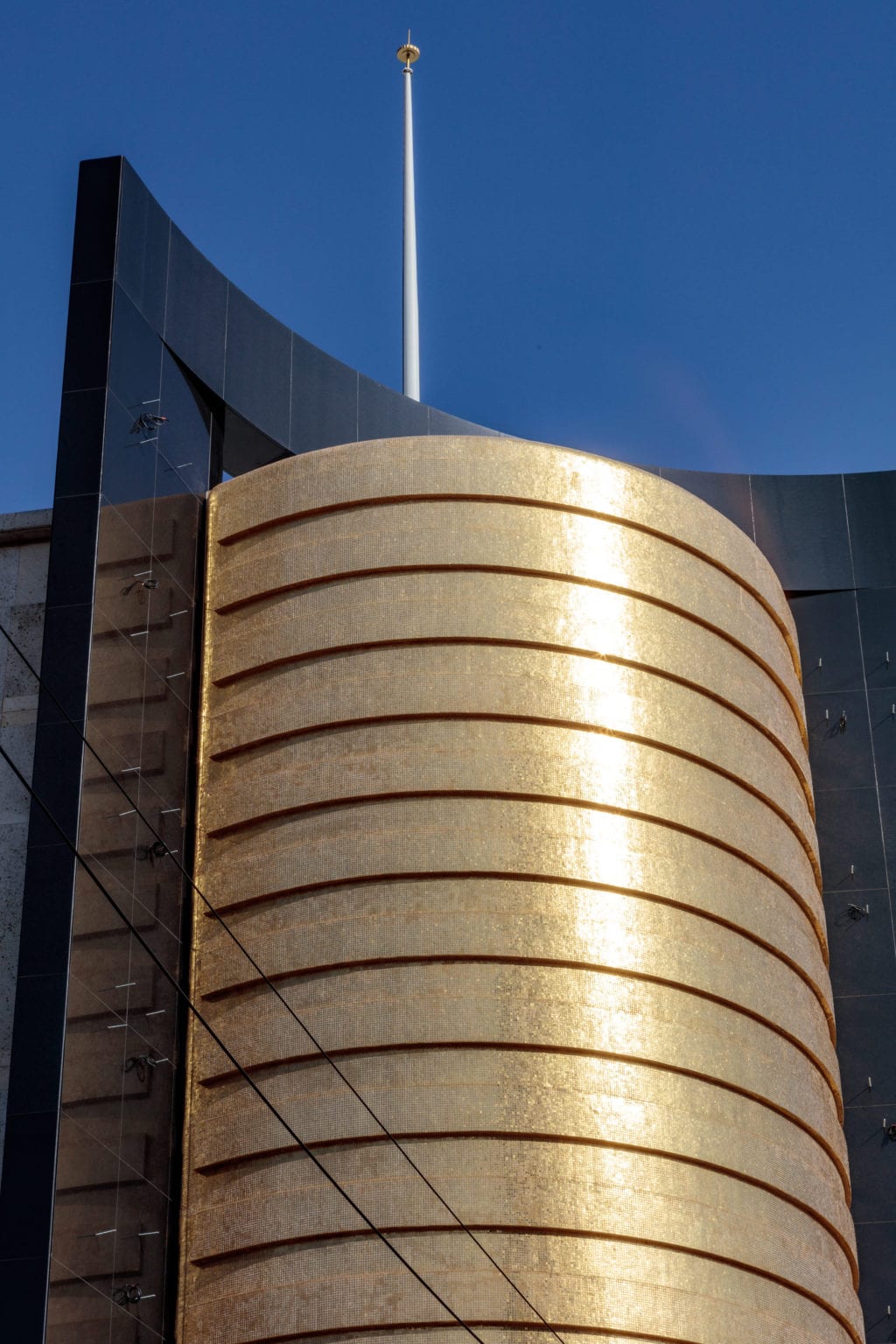
Preservation by Percentages
All told, the Saban building’s restoration crew retained, cleaned and repaired 95.7% of the original limestone cladding, 51% of the granite and 65% of the gold-glass mosaic. Involving everything from sleuthing through historical records, to testing solutions in laboratories, to scouring surfaces for defects with ultra-high-definition lenses, to good, old-fashioned elbow grease, the salvation effort has restored the May Company to its original grandeur, keeping its history alive for the next generation of Angelenos to enjoy and granting it a new chapter as the Academy Museum of Motion Pictures Saban Building.