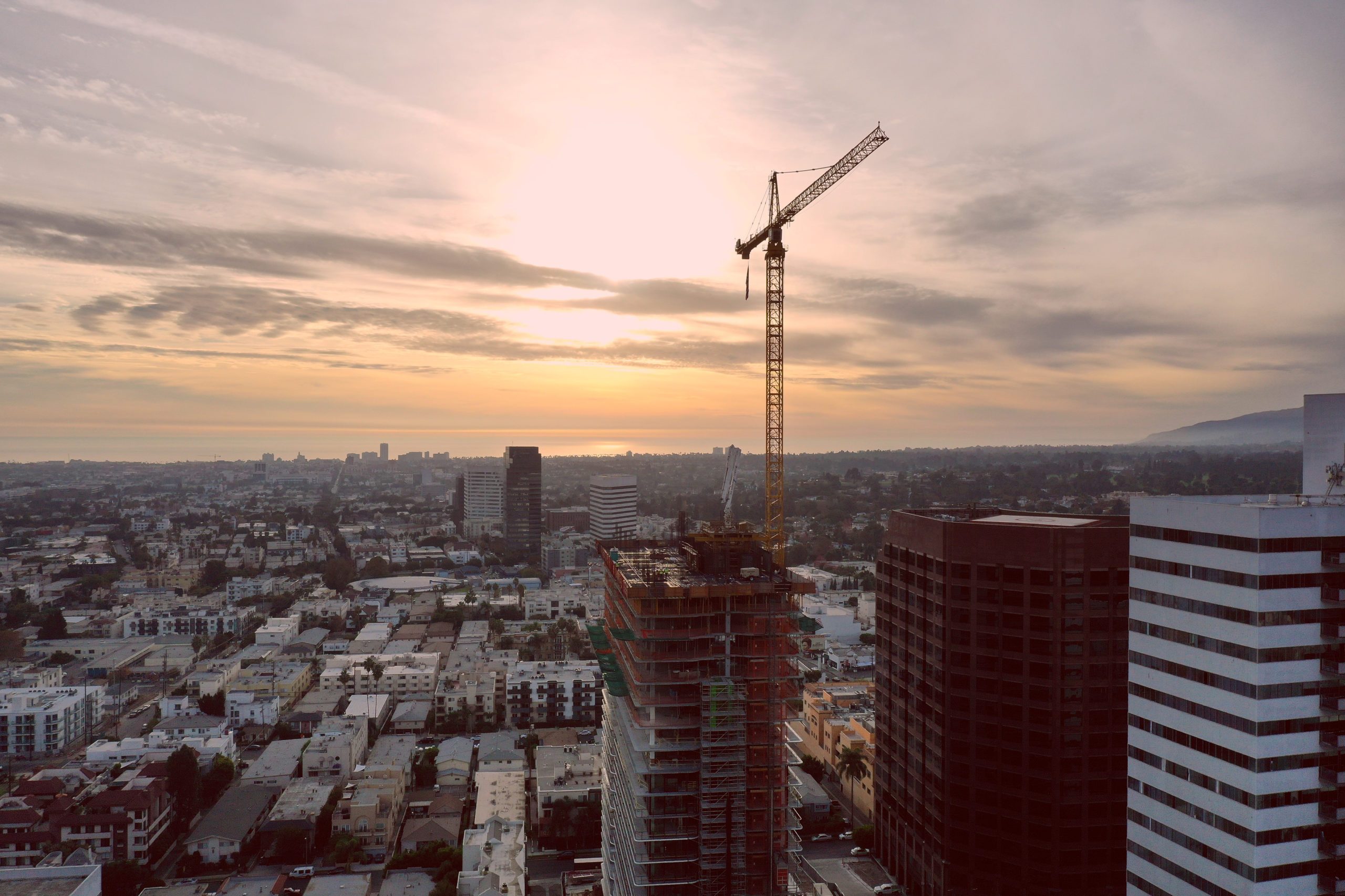
The Landmark Apartments’ Innovative Shoring System
The Landmark Apartments’ innovative shoring system keeps a garage operational while MATT demolishes a building-sized footprint inside it
The Landmark Apartments luxury residential tower is already living up to its name. The team has undertaken construction of what will soon rise to be the tallest building in West LA—right through the center of an existing, operational parking structure. For any team encountering a challenge of this scale, safety and determination must serve as guiding principles in pushing the project forward. Any doubts that this engineering riddle could be solved would undermine morale and limit creative thinking. So the Landmark team rallied and came up with a plan of attack that leveraged a massive, audacious shoring system as its main ally in structural safety.
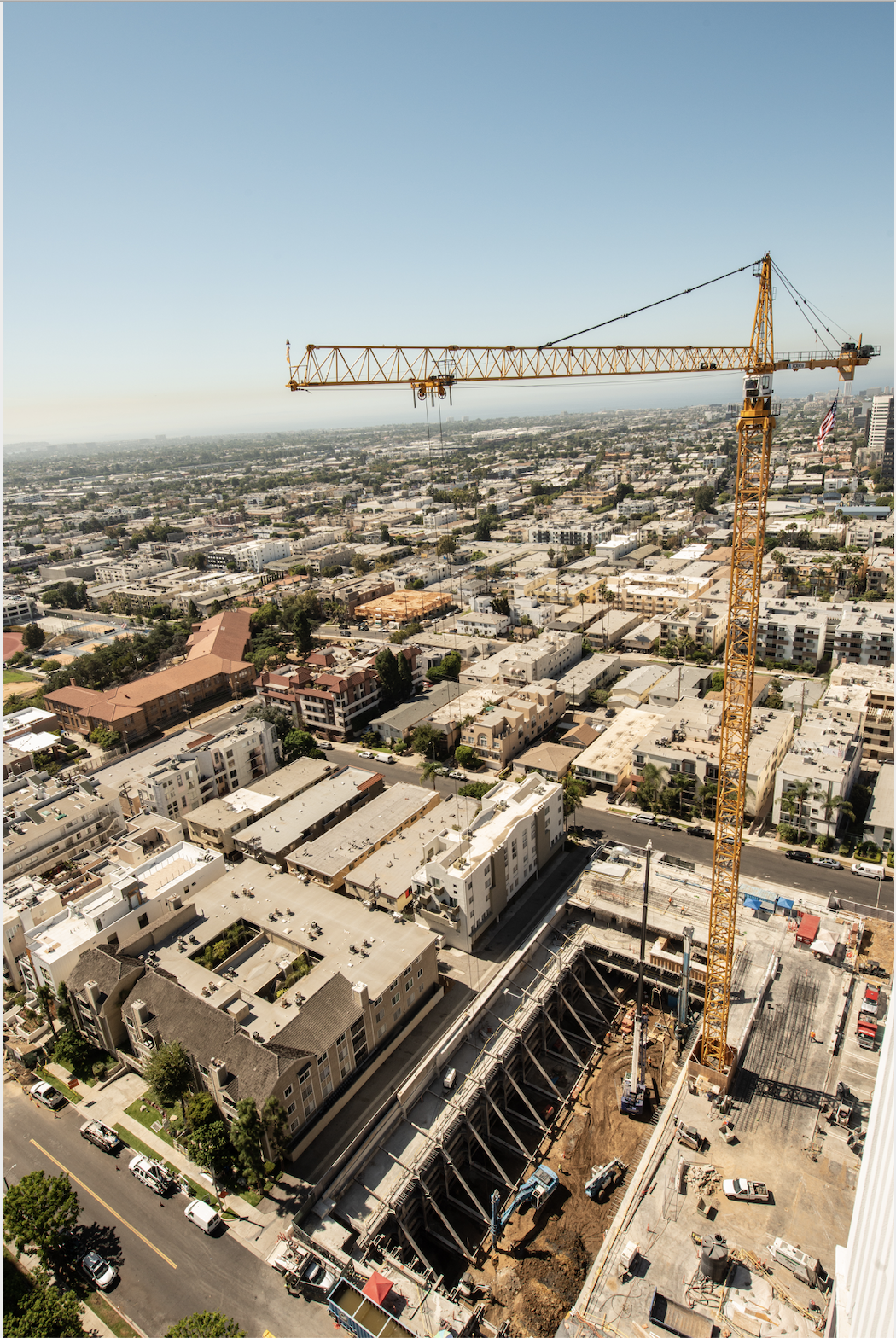
A Map of the Problem
Once complete, The Landmark Apartments will stand at a staggering 34 stories, outfitted with 376 sleek apartments boasting floor-to-ceiling windows, a charming park, a fitness center, a recreation area, a swimming pool and four levels of underground parking. It will undoubtedly attract discerning residents who long for a private oasis from LA’s busy streets, not unlike the Vision on Wilshire.
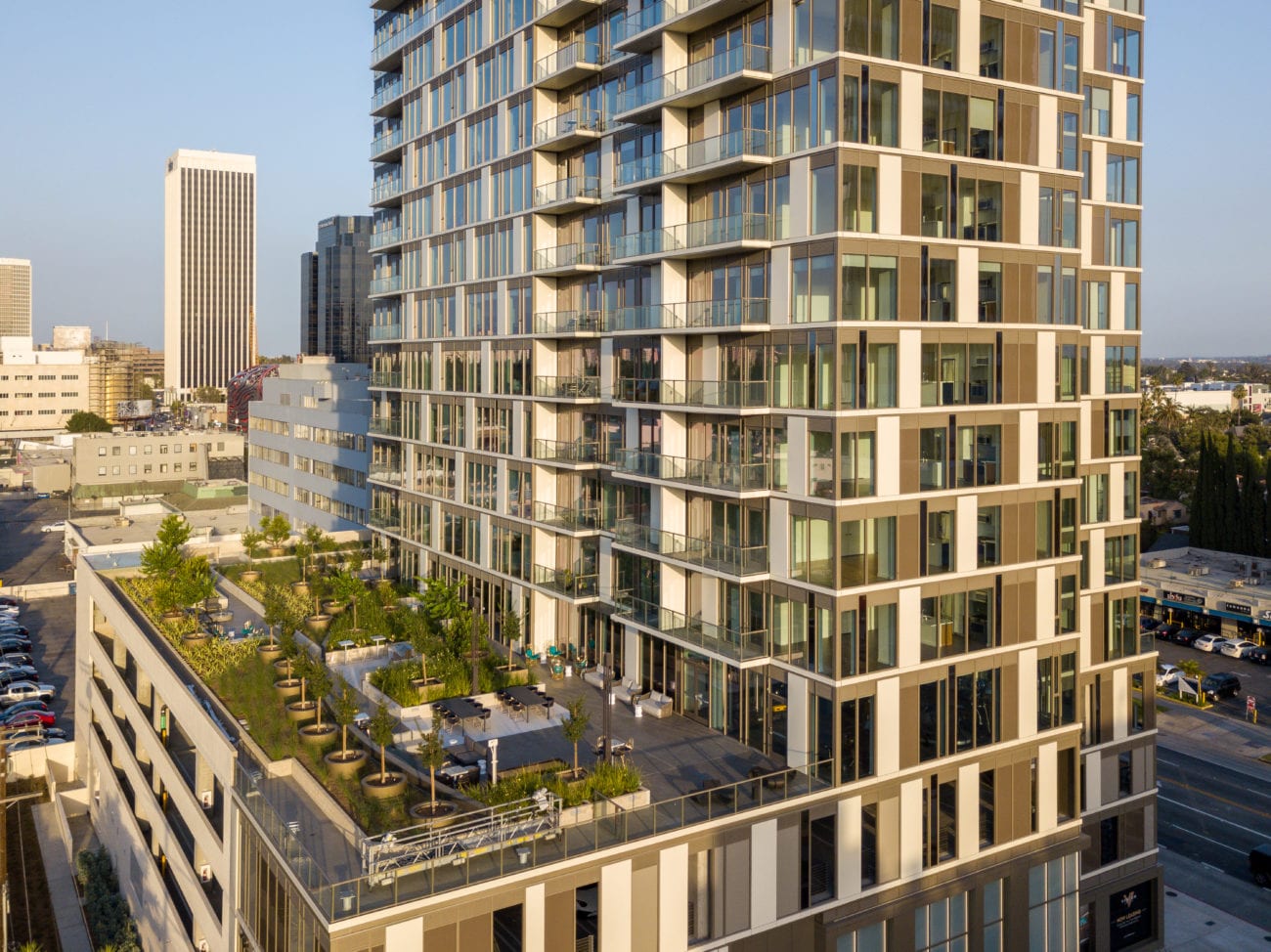
A Pavilions supermarket previously stood at the future site of the glass-and-steel skyscraper, which is slated for completion and first move-ins by late 2021. In order to prepare the site for construction, the crew had to surgically cut into the garage facility. Further complicating the challenge, the garage serves a neighboring, 18-story office building at the corner of Wilshire Boulevard and Stoner Avenue and needed to continue functioning normally throughout construction – keeping commuters and MATT personnel safe.
But the task at hand isn’t as simple as demolishing a section of the working garage and building upwards from the emptied core. If the team had started wrecking each floor without proper engineering measures in place, the entire structure would have lost integrity. This presented a major engineering challenge, one that sparked the creation of an extensive and critical shoring system. Without the system in place, the tower would not be able to go up within the existing garage.
Creative Engineering Solutions
Given the site logistics, solely using traditional tiebacks was not an option. The MATT team added value to the client’s vision by selecting a plan envisioned by engineering firm Plan B, who specialize in difficult demolitions. Much of their work takes place on the east coast, where they have to figure out such conundrums as how to hold up one side of a building to preserve a historic façade while the rest of the building gets demolished. Plan B’s staff decided on an elaborate shoring system in addition to tiebacks on the property that would preserve the integrity of the parking structure while work carried on within it. Plan B also coordinated to align the site’s existing parameters with the shoring elements and the future tower’s specs.
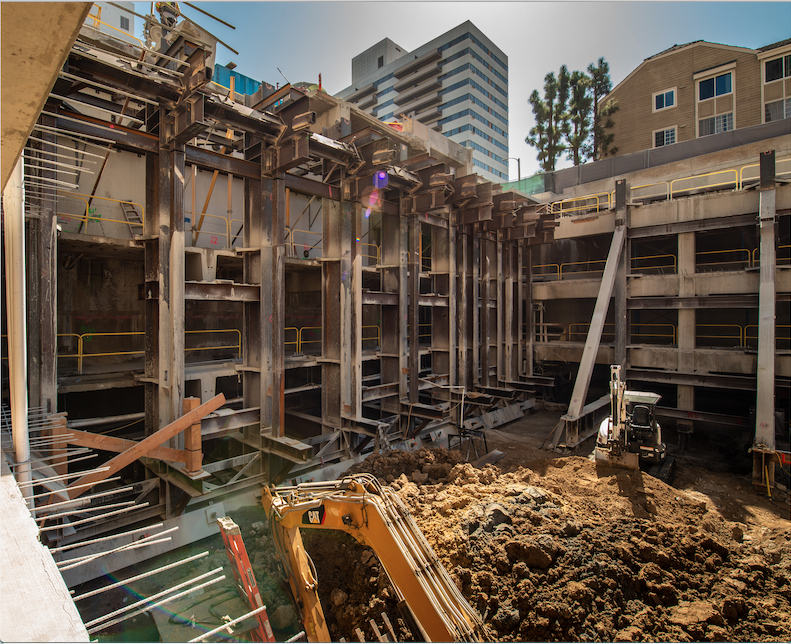
Problem-Solving For a Delicate Sequence
Before the crew began demolition work, they realized the shoring would need to perform multiple jobs at the same time. “Not only is it holding the walls up,” shares Nolan Caldwell, Project Manager on site, “but it’s also holding up portions of the deck where we had to demolish the foundation.” In effect, the current shoring is supporting the entire foundation and keeping the structure itself standing. The team spent painstaking months of meticulous calculation and simulations figuring out how to make this shoring system stand up to the processes of demolition and construction.
An initial method on the table was to use wire ropes that would tie back to major columns in the structure from sixty feet away. But such ropes are heavy, cumbersome and dangerous. “It’s like loading a rubber band,” Superintendent Sergio Mayorquin shares. To drive home the potential dangers, the team gathered around during a safety assessment and watched enough cautionary footage of the wire ropes snapping and sometimes even exploding that they came up with another technique involving tiebacks and strongbacks.
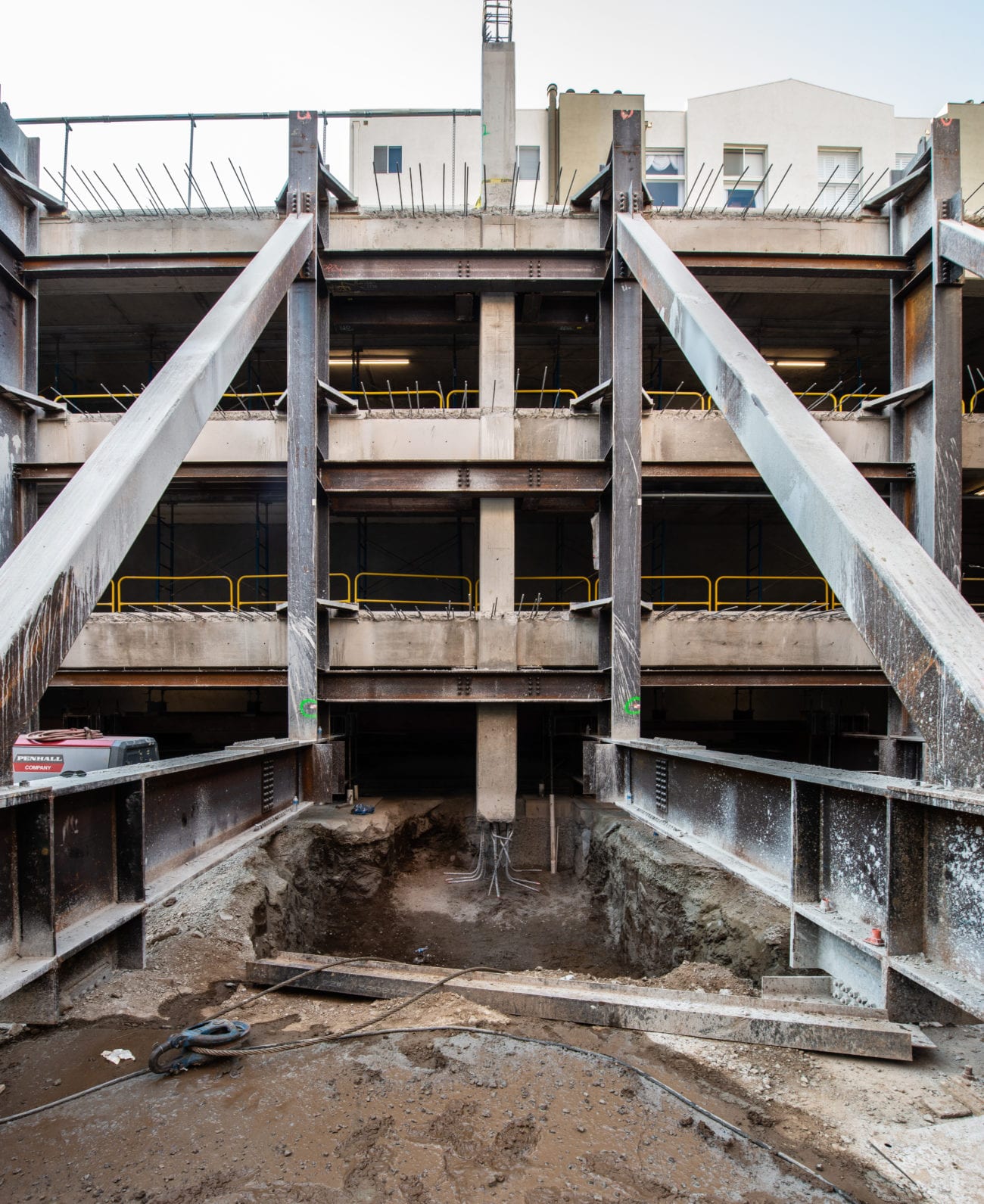
Setting Up the Tieback and Bracing Systems
Supporting the existing structure as these enormous, critical, high-strength tiebacks were put in tension was an “amazing” part of the operation, reflects Mayorquin. First, the team had to drill micropile supports 40 or 50 feet deep to uphold the existing footings within the tight confines of an underground parking structure that only offered 10’ of head clearance. The micropiles serve a similar function to tiebacks. To install them, the crew drilled straight into the ground, buffered the space with reinforcement, then poured concrete in. But further complicating matters was the water table; there was “practically a river underneath the structure,” Mayorqin recalls. Getting the rig to drill through the water as the river swelled twice a month, pumping the water out, keeping the systems unclogged, adding temporary filters—all of these unanticipated hurdles upped the ante on the difficulty level but yielded strong teamwork and communication. Once this whole process was done, the crew was safe and clear to demolish the core of where the new building would one day stand.
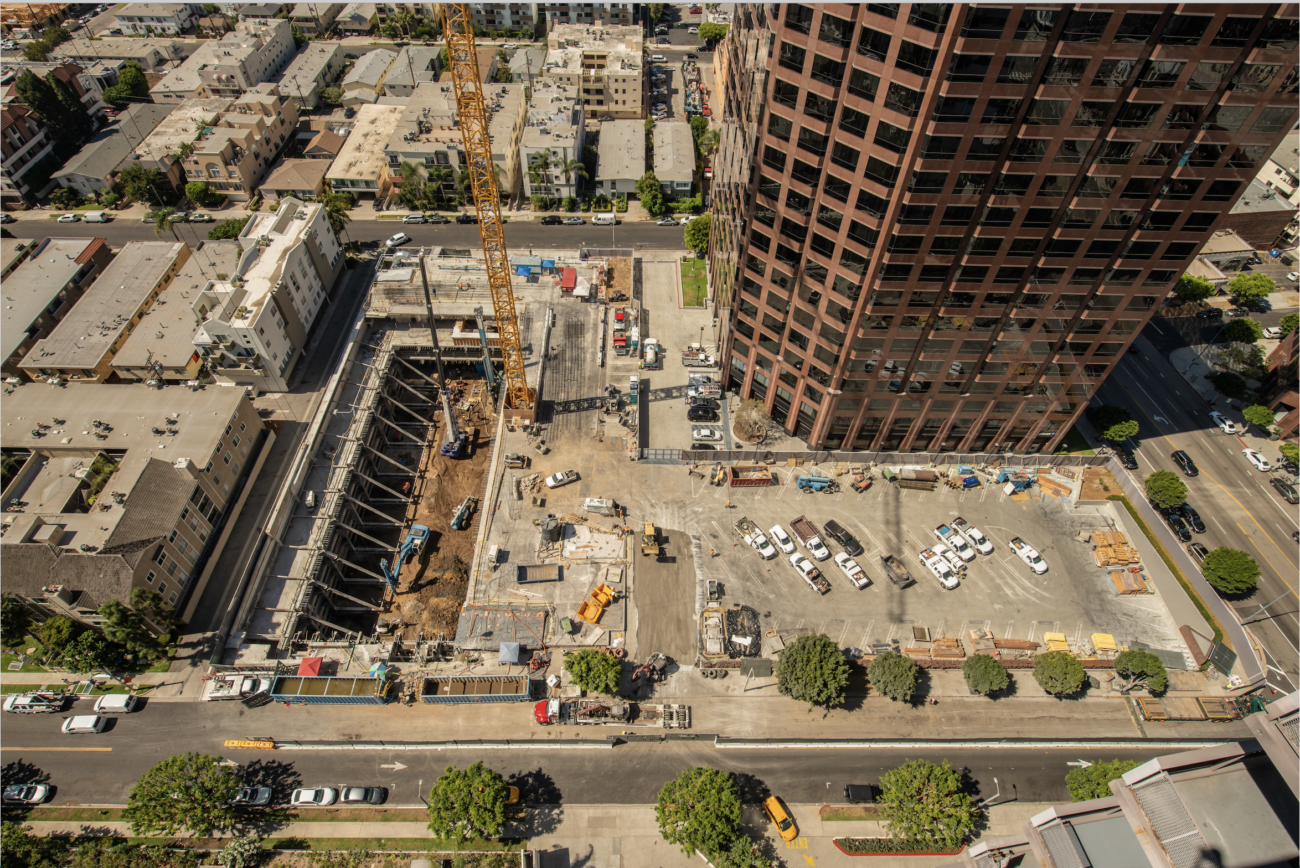
To get each massive tieback in place, the team installed a flat plate—a 1” thick piece of iron that welds all the way from where the tieback would begin to the strongback and waler beam supporting it. Mayorquin likens the push-and-pull play of tension to shooting a gun; when firing, the hand pushes and braces so that the force of the shot doesn’t cause excessive recoil. In the same way, the team used a system of tiebacks, strongbacks and walers to put pressure on the walls, but not so much that the whole system would lose integrity.
MATT’s team played out numerous iterations of the process of getting the structural steel beams in place for the bracing system beforehand to determine a practical sequence that maximized cost and schedule, minimizing any hassle to the client. They sat down with each latest design model from Plan B, crunched numbers and ideas and puzzled out how to fish the long structural steel beams into the space. They soon realized that the 50’ long pieces that help to form the shoring work were too large to fit, even with strategic access holes being cut into the existing, emptied-out Pavilions building. So they devised and then implemented two viable solutions: unbolt some and torch the others in half. Sectioning certain pieces allowed them to be maneuvered down through the four levels of the parking garage before the levels themselves were demolished, using a mobile crane. The pieces that had been severed were then either bolted or welded back together, depending on how they had been disassembled. At that massive size, each set of pieces could take a crew member an entire week to weld.
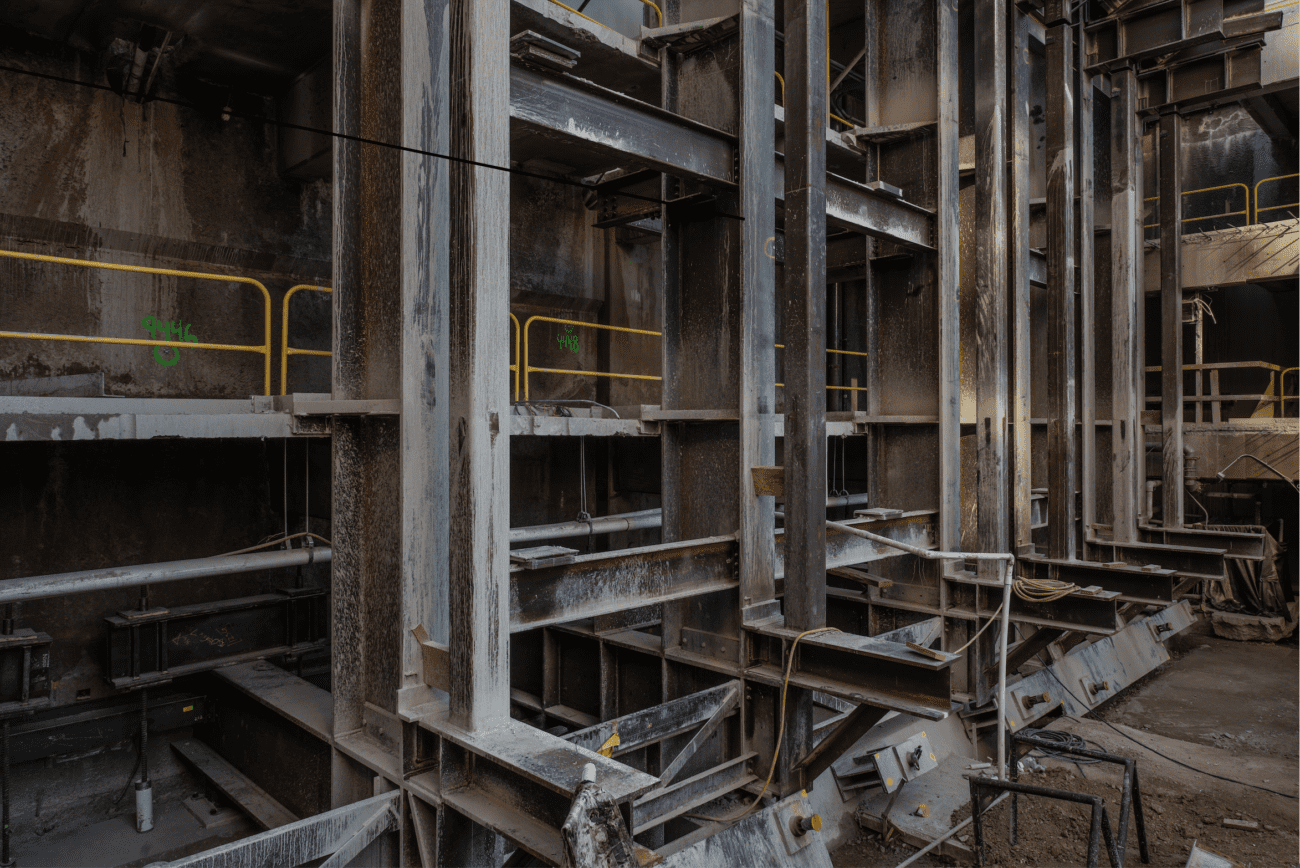
A Landmark First
“We haven’t done anything close to this,” Caldwell reflects. He adds that other MATT and Gensler team members who have spent over four decades in construction have never seen a shoring system like this in their entire professional tenures. The team embraced the unique challenge of having to devise a system to buttress the garage decks while kicking out the foundation, all without losing support within an existing structure they had not yet begun to demolish but soon would.
Mayorquin calls the shoring structure “an awesome piece of work. I’ve been on a lot of different jobs, but the shoring we had to put in place to be able to cut away the existing building and keep the integrity of what was left was very complex and interesting.” Not only did the shoring system call for out-of-the-box thinking in its developmental stages, but it also demanded on-the-fly solutions in the face of unforeseeable roadblocks.
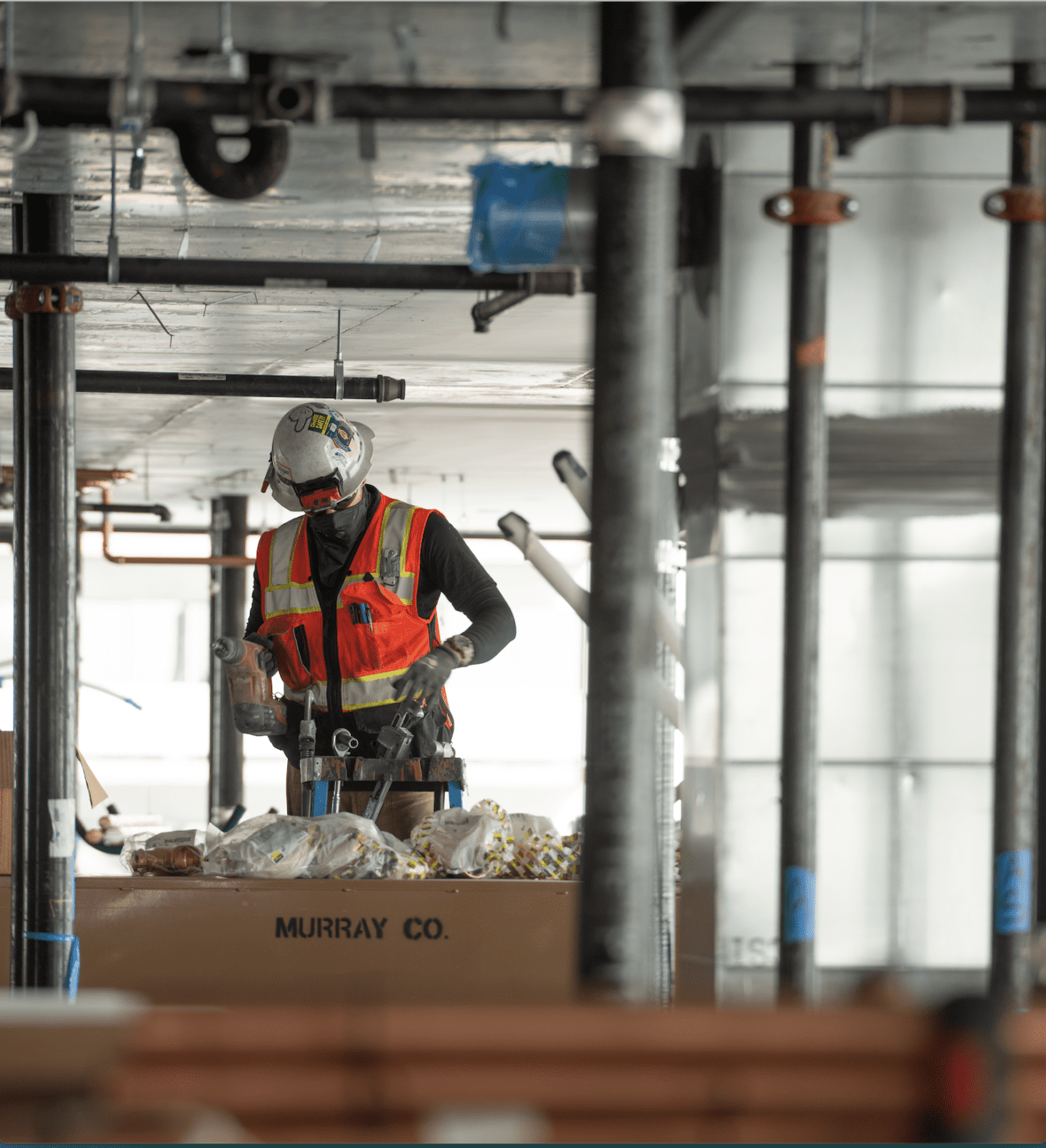
Part of what’s making this feat possible is the creative enthusiasm of everyone on site. From iron workers taking daily walks on site to problem-solve in real-time, to the Plan B team drawing elaborate models on grocery paper, Mayorquin was regularly impressed by the dynamic effort. “Most MATT field guys are builders and know how to solve problems and get it done,” he comments. There was never a doubt that, thanks to the grit and inspiration of all key players involved, they would solve this engineering riddle.